Identifying Hotend Thermistor
Fixing inaccurate readings of printer's hotend temperature
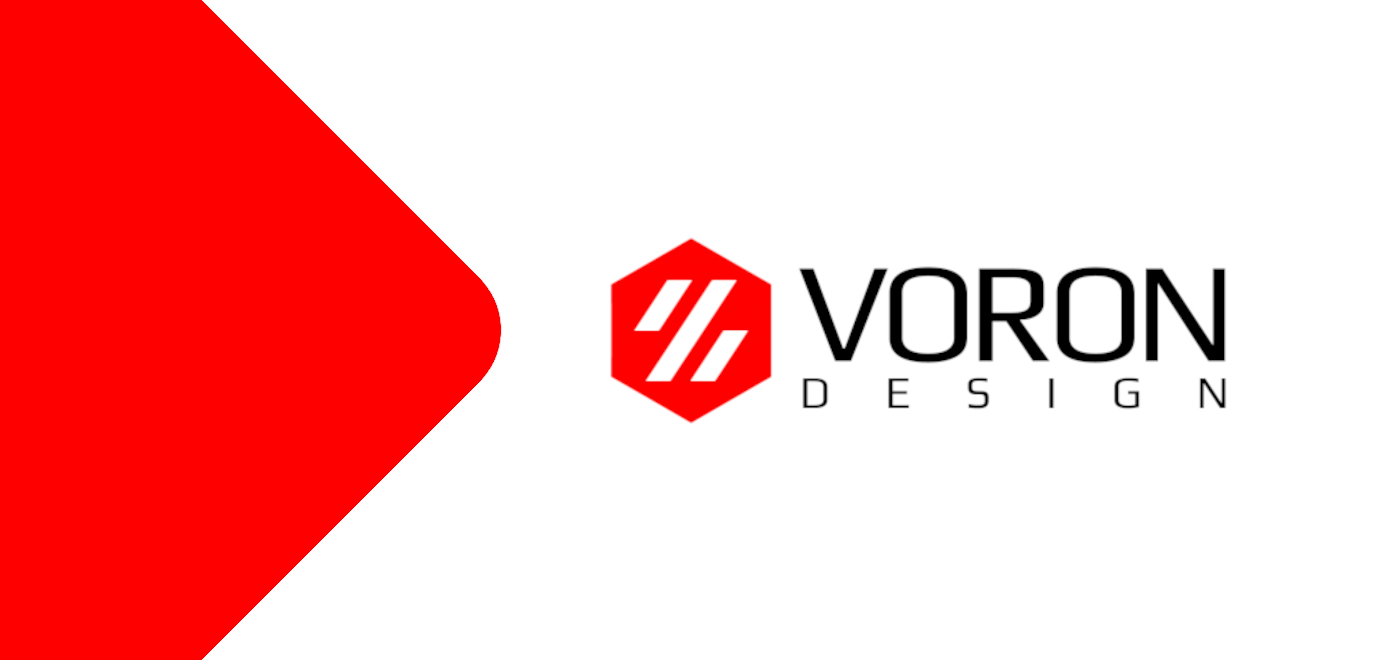
As a recent owner of a second-hand Voron 2.4, I’ve been exploring how it works and optimizing its performance (someone may affectionately call “calibration hell”). Early on, I noticed a significant issue with the hotend temperature readings: upon powering on the machine, the hotend consistently reported a temperature 12 degrees Celsius below room temperature. This immediately indicated a problem and explained why my prints “could have been better”.
Setup analysis
My initial step involved inspecting the cables on the EBB42 toolboard (a common BigTreeTech toolboard for Voron printers), consulting its BTT documentation, and reviewing my Klipper configuration files. The discovery was a clear misconfiguration: the hotend thermistor was incorrectly connected to the TH0 port on the EBB42.
While this port can be used for some thermistors, the EBB42 also features a dedicated MAX31865 sensor, which is specifically designed for PT100/PT1000 RTD sensors and offers significantly more accurate and reliable temperature readings. My suspicion grew that the previous owner had settled for the initial wiring rather than optimizing the setup.
Before changing the connections, I had to make sure about the kind of thermistor the printer had.
Empirical testing
Before looking at the results, here’s a reference of the possibilities I was expecting:
Feature | PT100 | PT1000 | NTC Thermistor |
---|---|---|---|
Change with temperature | Resistance increases | Resistance increases | Resistance decreases |
Resistance at 0°C | 100 Ohm | 1000 Ohm | Very high (the exact value depends on the model) |
Resistance at 25° | ~110 Ohm | ~1100 Ohm | ~100KOhm |
I then pulled out my multimeter and tested twice the two cables connected to the thermistor:
- The first reading at room temperature and got
1098 Ohm
- The second one after heating the sensor with my hands and got
1103 Ohm
Since the resistance increased with heat and the readings fell within the expected range for a PT1000, I could confirm it was indeed a PT1000 sensor.
Updating the configuration
My previous Klipper configuration was reading raw measurements from the thermistor on port TH0, showing fluctuating values too:
|
|
Therefore, I disconnected the PT1000 wires from the EBB42’s TH0 port, recrimped them into the appropriate connector, and reconnected them to the port utilizing the MAX31865. Finally, I updated the DIP Switch positions according to the BTT Docs
After that, my Klipper config looked like this:
|
|
The Solution and Key Takeaways
When I powered on the printer again, I noticed the hotend temperature reported a value very similar to room temperature, and it perfectly matched the bed temperature reading. That’s a definite win! Seeing those accurate numbers after all the troubleshooting is a huge relief.
With the sensor correctly identified and configured, the next crucial step was to run a PID Tune, as this process allows Klipper to precisely learn how to maintain a stable hotend temperature, optimizing its heating cycles. After completing the PID tune, I printed a test object, and showed how my print settings were off.
This whole process made me dive deeper into how different thermistors work, which was a valuable learning experience. It also reinforced a critical lesson: even with complex machines like 3D printers, breaking down an issue into smaller, testable steps is often the most effective path to a solution.